Below are the questions asked most frequently about ANT natural navigation. If you have more questions, please contact us.
Is ANT reliable?
Is natural feature navigation reliable? The short answer is yes. ANT is a highly reliable platform that is proven in industrial applications around the world.
As an example, the first ANT driven vehicle to go into commercial operation was an EMS Paquito AGV, installed at Dal Colle (Barilla Group) in Italy in 2009. This installation is still in operation today. Since then, over 6,000 more vehicles have been deployed, spanning numerous brands and types.
What types of vehicles run on ANT?
Over 150 different automated vehicle models run on ANT today. To explore these, visit this site’s Vehicle Finder. Since ANT offers virtual path following and obstacle avoidance modes, it suits not only automated guided vehicles but also automated forklifts and autonomous mobile robots.
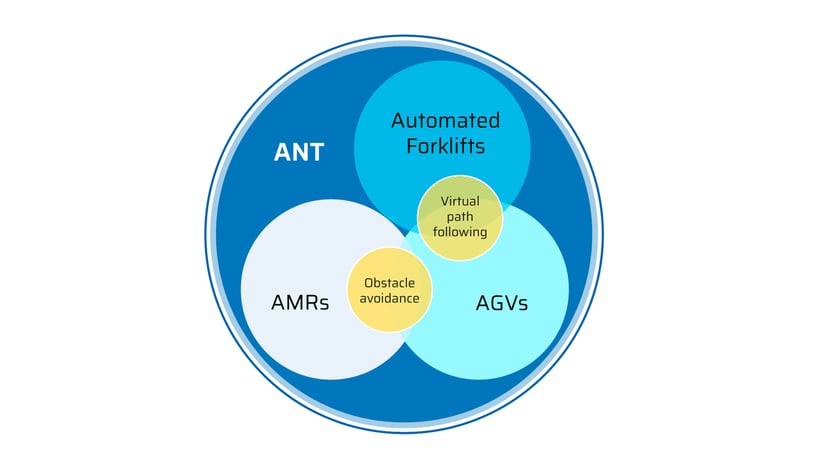
How long does it take to install ANT driven vehicles?
The installation (also called commissioning) of vehicles driven by ANT natural navigation is quick and simple.
Of course, careful planning is essential, such as deciding which tasks to automate, identifying pick and drop positions, defining routes, and setting traffic preferences. Your vehicle integrator can then use ANT software to fully simulate your operation. This will help you identify and solve issues upfront.
Once planning and simulation have been completed, the on-site installation of vehicles (mapping, programming routes and actions, and testing) is typically completed in a week or less. Larger installations with 50 or more pick and drop points may however take longer.
Does ANT natural navigation offer obstacle avoidance?
Yes. Vehicles driven by ANT natural navigation can be programmed to use virtual path following (stopping and waiting in case of an obstacle) or obstacle avoidance (whereby vehicles navigate dynamically around obstacles).
But do obstacle avoidance AGVs offer greater efficiency? The answer depends on the application. Generally speaking, path following suits industrial applications, whereas obstacle avoidance better suits mobile robot use cases.
Can ANT driven vehicles work outdoors?
Yes. With ANT everywhere, AGVs work with GNSS (with real-time kinematic (RTK) positioning) and the result is a seamless indoor-outdoor navigation system. It makes outdoor AGV and AMR operations just as robust and precise as those indoors.
A typical application is moving very heavy loads, such as tires or steel coils, between buildings or moving luggage on airport terminals.